The Arm® Cortex®-M33 processor is a popular choice for wireless systems designers looking to wring out every last microwatt from the constrained power budget of their IoT designs. That’s because it offers high performance while consuming very little energy.
Arm is an intellectual property (IP) vendor that sells its processor know-how to chip makers who then implement the design in their own hardware, either as a standalone processor or embedded as part of a System-on-Chip (SoC). The ultimate efficiency of the design of course depends on the hardware implementation, but according to the Arm datasheet for the Cortex-M33, it’s not unreasonable to expect a power drain of around 10 microwatts per megahertz while the processor goes about its business. And this comes with no performance compromise; this is a very powerful device. (For the technically minded, the Cortex-M33 boasts 4.02 CoreMark/megahertz).
The components offered to support an embedded processor in a low-power wireless design bring similar levels of efficiency. For example, consider the radio in a Bluetooth® LE or Zigbee SoC. It was not so long ago that these devices consumed several tens of milliwatts while sending or receiving data across the wireless link. That’s a huge amount when you’ve only got a tiny power budget and a user expectation of months of battery life. Today’s state-of-the-art short-range wireless SoCs do much more with less, offering greater range and throughput than the previous generation of products while consuming just a few milliwatts. Through design, material, and fabrication advances, the power consumption of processors, memory, radios, analog-to-digital converters (ADCs), linear regulators (LDOs), and the rest is a fraction of what it was just a few years back. That’s given designers the opportunity to markedly extend their product’s battery life or shrink its form factor by using smaller cells.
And yet, ask any two engineers to design a solution for a given application from the same box of low-power bits, and the resulting designs will have completely different battery life. And not by just a few percent. It’s not unusual for one design to be half as effective as the other at making the most of the battery’s energy. The difference comes down to the designer’s skill and experience. And that makes the person behind the product the most important influence on its power consumption.
What is it that the skilled low-power product designer knows that’s news to the rest of us? It comes down to hardware selection, good coding, testing, and sleep. Lots of sleep.
Peripherals Are Paramount
Experienced designers know that it’s not just the key components like processor, radio, and memory that determine energy consumption, peripherals are important too. When battery life is measured in months, even a lowly passive can shave off days of energy if it’s inefficient.
It’s hardly news that good design choices include peripherals with low-energy demands and -quiescent currents. But it’s also important to think about how the device will be used. For example, consider a built-in accelerometer; if the application only needs to know when it’s been inverted, then it’s good practice to ensure that’s the only time the accelerometer reports its position rather than continuously transmitting every tiny movement.
Care is also needed to select components with the minimum power dissipation. For example, buck/boost voltage regulators and LDOs all burn some power during operation so it’s important to select the most efficient while still supporting the needs of the application. This approach should extend to the less obvious parts of the circuit. For example, when a voltage divider is used to lower the voltage for an ADC it should be designed such that it dissipates the minimum amount of power through the shunt resistor. Another common failing is to design signal pulldowns such that they pull the voltage to ground but don’t minimize current leakage. That’s a persistent drain on battery energy and has a significant impact over the long term.
Good Code Saves Energy
Once the circuit is assembled it’s important that all the elements always run at the lowest energy consumption level possible. That’s not to suggest things should be frequently switched off because then the start-up cycles will take too long and compromise the user experience. But most modern low-power components have various standby and sleep modes where energy consumption is negligible, yet start-up latency is low. The skilled designer uses those capabilities to make sure that components are not expending energy unless they really need to.
In addition, the experienced engineer will check his or her code for triggers or interrupts that might generate unnecessary power consumption. To make their lives easier, these engineers typically structure their code to make it simple to read through. That makes it quicker to spot the lines of code that, for example, fire up peripherals when they’re not strictly needed or fail to put them to sleep once they’ve executed their task.
Once the obvious code errors have been eliminated, the skilled designer scrutinizes code for more subtle things like the processor entering a non-computation waiting loop—burning power while effectively achieving nothing—when it could be put to sleep. A second problem is a subsystem that does go to sleep as intended but is frequently awakened when it’s not strictly necessary. For example, a timer might be set to wake up the processor so that it can read some sensor data even if the application doesn’t need the information right then.
Another common mistake made by the less-experienced designer is to forget to disable the event logging that’s useful during development and debugging but is not needed in the field. The danger is that products leave the factory and spend their lives in the field switching on peripherals to log information that’ll never be used. But what will be used is the battery’s energy.
Check What’s Happening
Testing the average current consumption of an end-product is a simple way to estimate battery life. But it probably won’t tell the full story. Well-designed wireless devices continuously change between low power- and active-modes, and low duty cycles are very common. That means a short average-current test might miss infrequent peak consumption events that might still have a significant impact on the battery life.
The best way to get a complete picture is to take a detailed look at long-term power consumption using a full-blown power analyzer. That way the designer can clearly identify the transient power spikes that are common to low power wireless designs and make sure that each one corresponds with an activity that’s strictly necessary. The downside of this technique is that power analyzers are very expensive, very heavy, and very closely guarded by chief engineers.
There are some more portable—and considerably less expensive—equipment options for giving a reasonably detailed view of a wireless device’s power consumption. One example is Nordic’s Power Profiler Kit II. For less than $100, the designer can use this test tool to check out his or her product’s power consumption and then compare it with expected behavior using a complimentary online power profiler running a simulator. The estimate can be cross-referenced to the Power Profiler Kit’s results to highlight any anomalies which can then be inspected more closely to find their cause.
Conclusion
Tomorrow’s low-power devices will make today’s look like power-greedy monsters. But with current supply chain challenges, it will be a while until they’re readily available. The good news is that designers don’t have to sit still. Even the most skilled engineer is unlikely to have got everything right the first time. That makes a review of existing products worthwhile as it’s very likely to reveal some useful energy savings enhancements that can be passed on to users.
Author
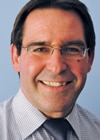
Steven Keeping gained a BEng (Hons.) degree at Brighton University, U.K., before working in the electronics divisions of Eurotherm and BOC for seven years. He then joined Electronic Production magazine and subsequently spent 13 years in senior editorial and publishing roles on electronics manufacturing, test, and design titles including What’s New in Electronics and Australian Electronics Engineering for Trinity Mirror, CMP and RBI in the U.K. and Australia. In 2006, Steven became a freelance journalist specializing in electronics. He is based in Sydney.